What’s the Difference Between Thermoforming and Injection Molding?
Plastic is everywhere and anywhere. It’s a versatile material that can be used across a wide range of applications. It can be in your home, in your surrounding, or in your body. However, you’ll think that all plastic are the same—they’re not manufactured in one way!
Most people think it’s done in one process, but it’s not. The most popular manufacturing processes for creating plastic is thermoforming and injection molding, two different processes that can be used depending on its application.
If you’re asking what’s the difference and what saves you more from costly manufacturing, let’s get to know the difference between the two.
What is Thermoforming?
Thermoforming, in easy words, is adding heat to achieve a certain form. It’s the process of forming a heated plastic sheet to the surface, applies the process of vacuum and air pressure to obtain the desired space needed.
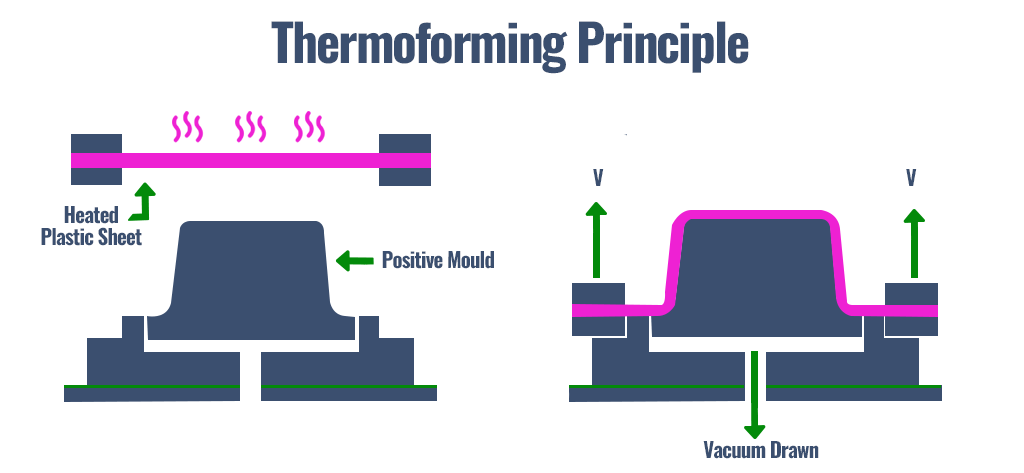
Products with unusual shape and design are the typical examples for thermoformed packaging formed through the vacuum process, like car dashboards and even a simple tray.
Thermoforming, after all, is for the people who want a cheaper and faster solution. Thermoforming molds are done 10 weeks earlier than traditional molds, and uses 3x cheaper material than any other plastic packaging solutions.
How about Injection Molding?
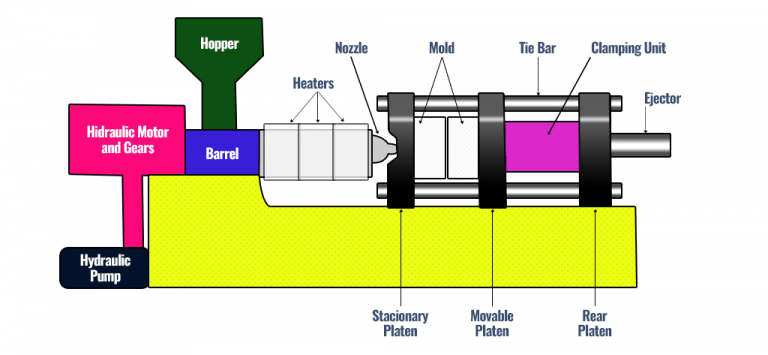
This process works by feeding plastic pellets into the hopper of the molding machine. The pallets are fed into a rotary screw that heats and melts the plastic, then the same rotary screw action injects the molten plastic into the closed mold where the plastic hardens into the final shape.
It’s ideal for large-volume orders and mass productions that need to replicate the same thing over and over again for a million time.
So what’s the verdict?
Thermoforming is a process that we take pride in Plastiform, as it has advantages in economical prototyping, lower cost tooling, shorter lead times, and the ability to easily R&D to optimize the final part.
Normally, thermoforming is done for small-volume production and larger-scaled designs, and it’s mostly good for prototyping and those that pose a challenge in packaging but wants to ensure quality and safety. It makes it easier for you to get your packaging design approved by retailers while getting the attention of customers that boost your products and overall sales.
You also get to ship more products at a faster pace.
On the other hand, Injection molding is used for small parts for large-volume productions that requires accuracy and precision where you’ll need it to replicate the same product for a million times.
Depending on how you need a plastic material, the process will be entirely different and will be up to you to choose from. For thermoformed packaging, don’t forget to check out Plastiforms, filled with safe and quality packaging.
No matter what industry you’re in, our battle-tested custom packaging will definitely help you out.
Have questions? Want to request a quote? Send us a message today!